In the world of CNC there are so many options to choose and when it comes to tool selection it is no different. Tool selection is critical when it comes to achieving a desired surface finish, tool life, or cut speed of a specific material. Tooling manufacturers go to great lengths to engineer tools to deal with specific aspects and properties of certain materials. Selecting the right tool for the job could determine whether a job fails or succeeds.
This blog discusses all aspects of CNC Tooling, helping you to become a tooling expert in no time.
The Different Tooling Materials
Tooling manufacturers go to great lengths to engineer tools out of specific materials, each of which have unique benefits. Here at AXYZ, the majority of the tooling we stock is solid tungsten carbide, this is a standard industry tool at a competitive price. We have also introduced a range of polycrystalline diamond (PCD) router bits into our portfolio for users that require an extremely high edge quality.
Solid Tungsten Carbide Router Bits
Tungsten carbide cutters are made up of very hard particles of tungsten carbide bound together with metallic cobalt. Bits produced with this material are very strong and durable and tend to stay sharper longer than HSS tools. You can find these tools at CNCshop.com
Polycrystalline Diamond Router Bits
Polycrystalline Diamond (PCD) tooling is composed of diamond particles that are sintered with a metallic binder at extreme temperatures and pressures. This manufacturing method allows diamond particles to be fused onto a carbide substrate and creates the hardest and one of the most abrasive resistant materials used in CNC router bits. You can find these tools at CNCshop.com
PCD v Solid Carbide: What’s the difference?
The cutting edge of a PCD tipped router bit lasts much longer than carbide for extremely long life.
Depending on the material being cut, PCD tooling has been known to outperform a carbide tool by a ratio of 300:1. However, to be conservative in your buying decision, we suggest you base your expectations on 25:1 ratio over carbide tooling.
When using PCD tooling for cutting composite panels and fiberglass, tool life can be up to 25 times greater than conventional carbide tooling.
- Tool life up to 25 times longer when compared with carbide tooling
- Saves time and money
- Consistently good component surface finish
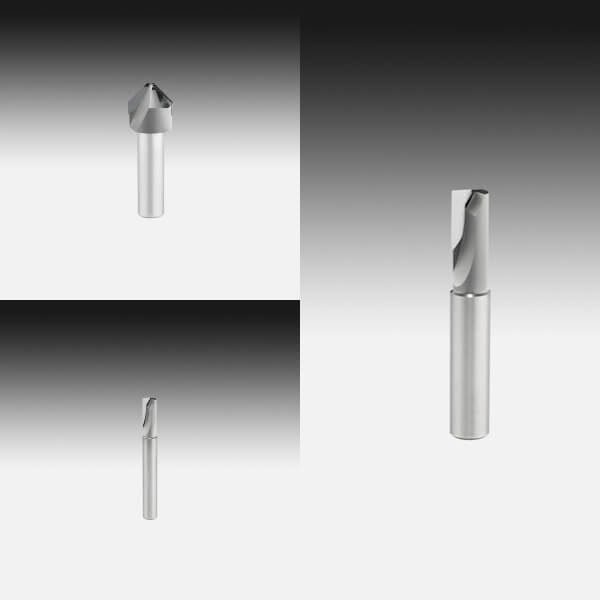
There are other tools on the market that can be used, here are some examples:
Carbide-Tipped Router Bits
Carbide-tipped tooling provides some of the edge longevity of carbide with the lower cost of a steel base. Carbide tipped bits are only available with straight flutes
High-Speed Steel (HSS) Router Bits
HSS is a poured material, chemically and metallurgically bonded together. The steel is processed from raw ore and heated to a liquid stage where several minerals and elements are added to improve the internal structure. Typically, HSS tool life is not as long as carbide.
Ceramic Router Bits
This tooling is worth considering when carbide’s life is not acceptable. The major consideration with these tools is the cost of the coating materials. Similar concept to PCD tooling.
Geometry and Material Types
In order to achieve your desired edge quality, choosing the right geometry is extremely important. The geometry of the tool determines the direction of your chip flow, choosing the wrong tool type can burn, chip or damage your material, rendering your workpiece useless. This guide will help you make the right decision for your chosen material.
Straight Flute
Use for wood and plastic operations. The straight flute design, in single or multiple cutting edges, produces a clean finish. The harder the material, the more cutting edges are recommended. The straight flute does not allow for the lifting of material out of the cut.
Spiral Flute
Use for aluminum, wood and plastic operations. The up-spiral flute is especially good for chip removal. When cutting aluminum and plastic, re-melting of the chips is the primary source of poor cut quality.
Use single spiral flute tools for faster feed rates in softer materials. The single-flute cutter typically has lots of room for chips, but the single cutting edge limits either the feed rate or the hardness of the material to be cut. These types of cutters are especially recommended for plastics.
Use double or triple spiral flutes for a better finish in harder materials. Double-flute bits provide a smoother cutting action because the chip load is smaller than a single-flute cutter for a given feed. This allows harder materials to be handled.
Upcut spirals are the most popular type of spiral fluted tool. Use these for grooving or slotting, for upward chip evacuation and best finish on the bottom side of the part. These bits allow for rapid cuts since the tool clears the chips away from the material. This type of tool is not recommended for softer materials because of the ragged finish that can result on the top surface. This type of geometry is used whenever the best finish is needed on the bottom side of a part.
Downcut spiral tools are best used for thinner materials which will be pushed down into the machine bed rather than being lifted with an upcut spiral. They are also best for leaving a good cut finish on the top surface of cut parts. Note that the cutting speeds usually have to be reduced because the chips are pushed back into the material. Chip extraction is generally less effective with this type of tool than it is with upcut spiral tools.
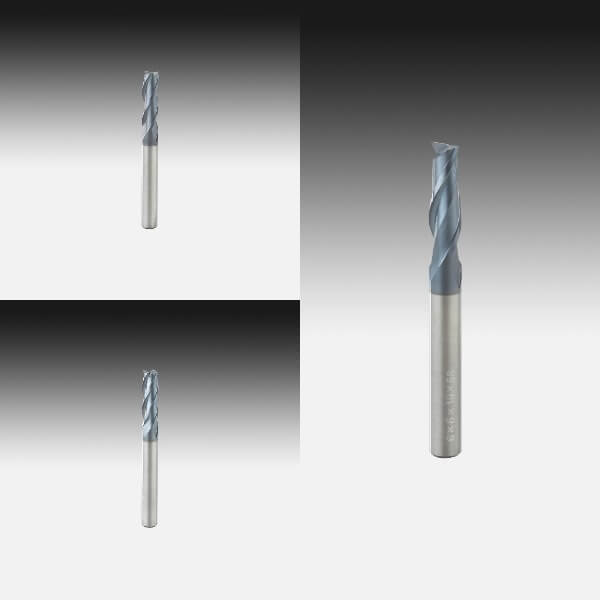
Chipbreaker
Use for wood roughing or hogging operations. The chipbreaker is designed to break up chips for fast, clean and efficient removal whilst reducing overall chipload.
Compression
A compression bit is the combination of both upcut and downcut spirals. Typically, a compression spiral has an downcut single, double or triple flute at the tip of the cutter, approximately one third of the cutting length. The remaining two thirds is ground to give an upcutting shear.
By combining both geometries, you achieve a win/win situation. The bottom of the material is pulled upwards while the top of the material is pushed downwards thus eliminating the risk of damaging the laminated surfaces. When run at full depth, the bit leaves a sharp, clean edge on both sides of your workpiece.
A compression bit can be a little more expensive than standard router bits, however here at AXYZ we recommend them as an essential tool when processing double laminate wood materials.
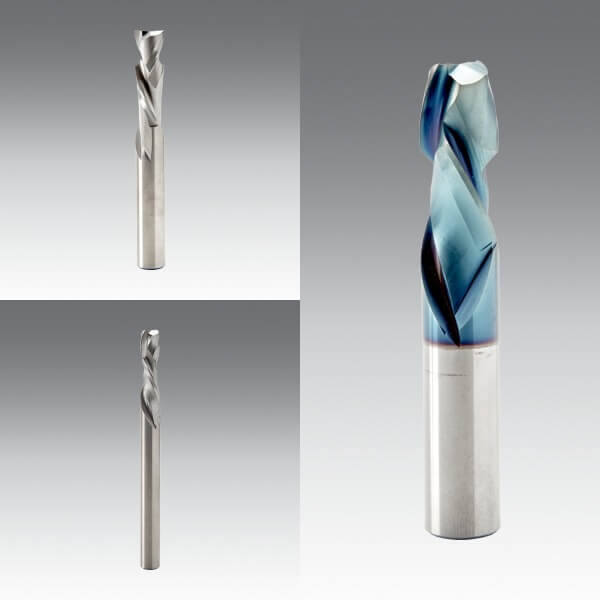
Ballnose
Ballnose tools have a spherical tip designed to be used for 3D machining operations. By selecting a suitable tool diameter and an appropriate stepover (the distance between adjacent tool passes) it is possible to achieve a smooth and accurate 3D surface on most materials. Some ballnose tools are coated to give them extra durability and should be used when cutting more abrasive materials.
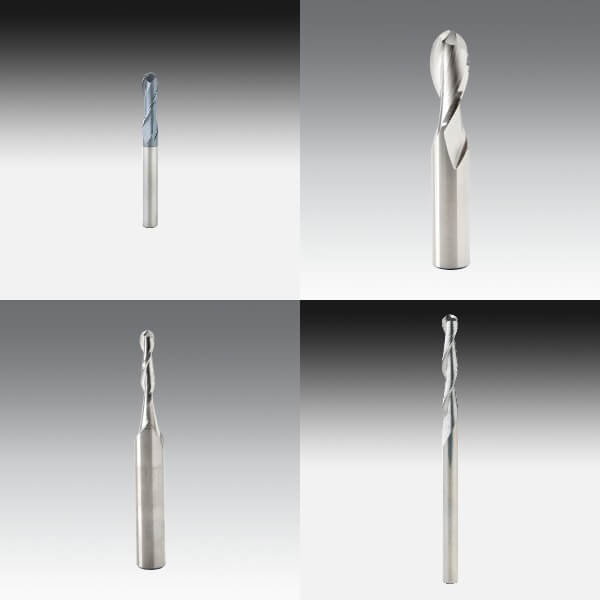
Grinding Burr
Made from solid carbide, these tools have multiple diamond shaped cutting flutes leave a smooth finish and produce small chips for easy extraction. These are often referred to as grinding burrs because of the high number of cutting edges, they are durable and work well on abrasive materials that may be difficult to machine using conventional single or twin fluted tooling.
The cutting flutes on the tip allow these tools to be used for plunging as well as profiling. These tools are ideal for processing fibreglass, carbon fibre and other composite materials.
General Tooling Recommendations
Finally, here are some general tooling recommendations that will provide a good starting point for cutter selection:
- Single Edge Router Bits: Use when speed is the primary consideration and edge quality is less important.
- Double Edge Router Bits: Use when edge quality is the primary consideration.
- Upcut Spiral Router Bits: Use for grooving, slotting or when fast chip removal is required.
- Spiral, Straight or Shear Router Bits: Use for natural woods, composites, particleboard, plywood or MDF.
- Spiral Router Bits: When finish and/or available horsepower are problems.
- Cutting Length: This is very important when demanding high edge quality. Use the shortest cutting length allowable, based on the material thickness. Using a tool with a cutting length that is longer than required can cause vibration, deflection and an inferior finish.
- Cut Length and Cut Diameter: In general, the cutting length should not be more than four times the cutting diameter. Bits with a cutting length over four times their diameter will be subject to increased breakage.
- Cut Diameter: Use the largest tool diameter possible for the design to be cut for increased rigidity, quality finish and long tool life
For all your tooling, parts and consumable needs, visit CNCShop your one stop shop for all things CNC.
Author: Abdullah Umair is an application specialist for AXYZ, a global manufacturer of CNC router and knife systems. Abdullah has covered many areas during his spell at AXYZ to ensure he has gained holistic exposure to both the needs of customers and the functionality of the machine.