Signmaking companies that turn out customized work for their customers have more options today when it comes to programmable computer numerical control (CNC) routers. With so-called ‘hybrid’ CNC machines, all of the cutting tools that might be required for a wide variety of materials are mounted and ready to be used interchangeably.
CNC hybrids are a relatively new trend. For small sign shops, especially, they can improve efficiency and reduce downtime, as there is no need to manually change out the cutting tools.
The key to versatility
CNC hybrids are becoming increasingly popular as a niche technology because of their versatility. They allow a broad variety of flexible and rigid materials to be cut on a single machine, rather than having to purchase two or more different models for different types of jobs.
The key to this versatility is in the design and engineering of hybrids, which can accommodate both the standard router bits typically used for hard materials and knife cutters for softer ones. With only minimal setup time, the router itself can switch from one type of cutter to another, after being programmed.
Thus, installing a CNC hybrid can make a lot of sense for sign companies, particularly smaller shops where floor space is at a premium and capital expenditures are made only with the utmost caution.
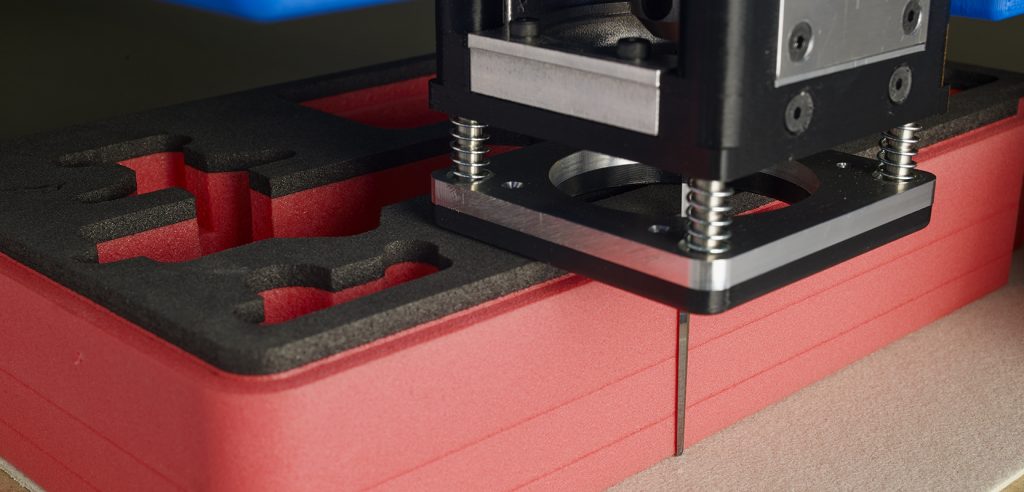
Merging technologies
CNC routers, which themselves began as plotting machines before the cutters were added, have now been around for more than 40 years. They use digitized point-to-point ‘maps’ to cut shapes along the X and Y access and to drill holes along the ‘up and down’ Z axis.
As the number of materials requiring precision cutting and close tolerances grew, a CNC router’s standard carbide bit would not always do a sufficient job. This was especially the case with softer materials, where the bit would tend to grab and distort the edge it was cutting.
This is where knives came in handy. Since the cutting surface area of a knife is much smaller than that of a bit, there would be (a) less chance of bunching up the material during cutting and (b) more chance of staying within the required measurement tolerances.
For sign shops that used a variety of materials in their production department that needed finishing, the market demand for both CNC routing and knife cutting could mean having to lay out additional funds—and find additional room—for at least two cutting machines. This problem is one of the main reasons CNC hybrid technology was developed later on.
Operator training
In today’s sign and graphics shops, the range of materials can include vinyl, aluminum, hardwood, polystyrene (PS), all types of plastics, fabrics and even leather.
All of these materials’ finishing requirements have been addressed with CNC hybrid machines, but it is not enough merely to have the equipment on hand. Operator training is also needed.
This is why it is important to work with reputable suppliers, who will provide initial on-site informational visits, subsequent technical updates, prompt phone support, software revisions and/or online training, as necessary.
“Our training took less than two days,” says Bill Stender, owner of SF Landmark Signs in San Francisco, Calif., after investing in a CNC hybrid router with a three-head configuration. “Our employees couldn’t wait to start using this more machine. Since then, we have had very few issues and they were quickly resolved.”
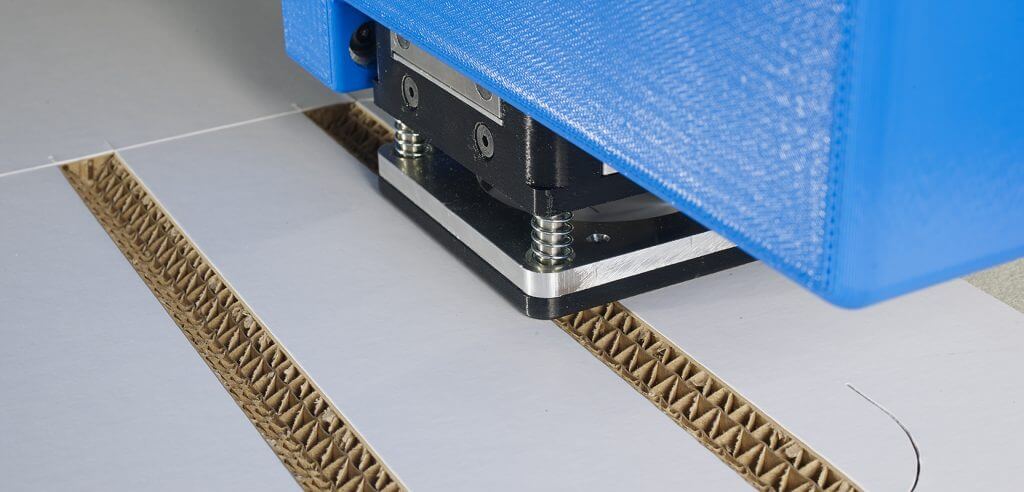
A sound business decision?
Many sign shops start out these days with the purchase of an inkjet printer that can place a graphic image onto sign stock, which then must be cut to shape. In a low-volume ‘one-off’ shop, using hand tools for the cutting may prove economical, but once the business starts to expand, there is a need for greater automation, duplication and reliability.
At that point, the question arises as to whether the digital cutting process should be added in-house or outsourced to a specialty subcontractor. The differences between these two options must be weighed not only in terms of time and money, but also with respect to quality control. Anytime a sign is sent somewhere for cutting, after all, there is both a transportation cost and an additional opportunity for damage during shipping. And when timelines are tight, damage to sign stock could result in the loss of a customer. All of these factors need to be considered in the ‘equation.’
In any case, most signmakers decide at some point in the growth of their business to make the leap to in-house digital cutting. The timing is a matter of ensuring there will be a payoff, i.e. when their upfront investment breaks even and then starts to generate profits.
Indeed, adding a CNC router to a sign shop’s finishing department is commonly the final piece in the business puzzle. With that in mind, the decision to invest in CNC hybrid technology should be made with an eye to the future—will the machine still ‘make sense’ for the business in three, five or 10 years’ time?
Other considerations
There are also a number of other issues to consider in terms of taking the ‘long view’ before investing in CNC hybrid technology.
One of these is, of course, the sign shop’s inkjet printer, which will help determine what size of cutting table the CNC router should have. If the printer is capable of outputting 1.8-m (6-ft) wide graphics, for example, then a 1.2-m (4-ft) wide hybrid router is probably not the right choice. That would introduce an unnecessary limitation and potentially drive clients’ business elsewhere, i.e. to shops with the capabilities for accurately cutting larger signs and graphics.
Another issue is a router’s control system—how operator-friendly is it and how much training is needed? If the principal operator is ever sick at home or away on vacation, after all, then backup personnel will need to be able to step in, with a minimum of disruption and downtime.
The aforementioned benefit of versatility is also variable. The CNC hybrid machine’s capabilities should match the sign shop’s requirements as closely as possible, whether for longer runs where four to five pieces are the same or for custom ‘one-off’ projects. And it may well need to cut six or more different types of materials in the course of any given day.
Software can help minimize setup time for these various materials, which is a prime consideration for novices. No one wants to have to turn work away because the setup routine for a new project would cause an inordinate amount of downtime in the production schedule.
It is also important to make sure the cutting software is compatible with the sign shop’s existing graphic printing software. Otherwise, a new capital purchase could end up compounding problems, rather than fixing them and reducing labour costs and lead times for in-house jobs.
Finally, as mentioned earlier, the supplier’s level of support needs to be evaluated before going ahead with the purchase. If a problem arises, it should be easy to reach someone who can perform diagnostic services remotely, rather than wait for them to arrive on-site, so as to resolve things quickly.
That said, support should not become a ‘crutch’ for an unreliable machine. Some CNC hybrid models can operate problem-free for months on end, while others seem to require constant maintenance. It is a good idea to do the homework and check reviews from experienced users.
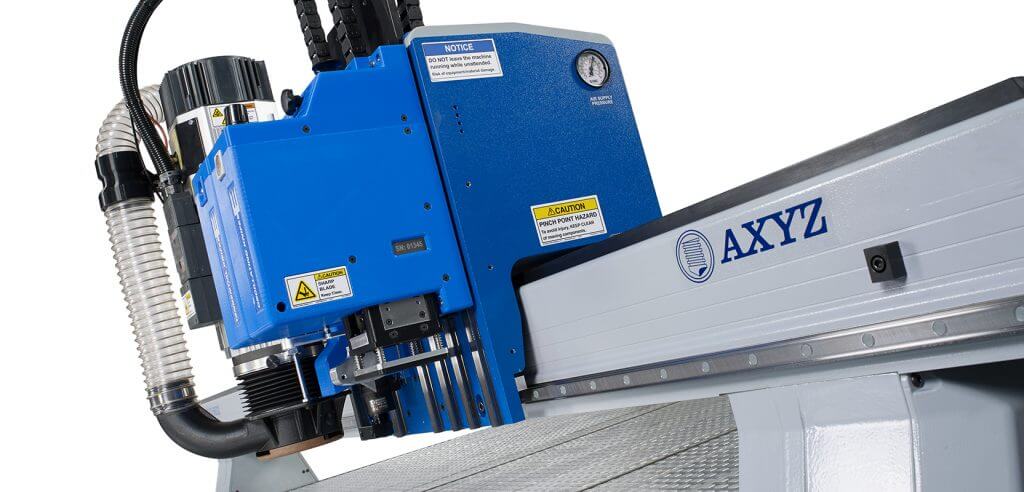
The automation equation
Much as digital inkjet printers have automated the process of graphic production, having all of the cutting options available on one CNC table, with an automatic tool changer to do the swapping out, is a good place to start in terms of automating the process of graphic finishing.
The less an operator has to get involved, the better, as there are fewer opportunities for human error and reduced downtime. Once the user presses the button, he/she can move on and select a different tool for the next material that needs to be cut.
CNC hybrids have been refined over the past decade with these purposes in mind. They have been redesigned based in large part on feedback from signmakers and other professionals who have needed to change cutting tools more efficiently than in the past.
With a manual tool change, there can easily be five to 10 minutes of downtime. Supposing there are eight to 10 tool changes a day for a typical sign shop, the time savings of a CNC hybrid will quickly add up over the course of a week.
In turn, more new jobs can be accepted and, for that matter, shorter lead times can be quoted to customers in the first place. In today’s market, shorter lead times can lead to more referrals and a stronger reputation as the ‘go-to’ shop in town.
Finding the right time
If CNC hybrid technology can be judged a viable choice, based on a sign shop’s workload and logistical factors, then there is no longer any reason to purchase two routers, one dedicated to standard bits and other using knife cutters.
It is a question of meeting customers’ needs. For the signmaker, this means doing the homework, keeping an eye on the future and determining which system is the best option.