AXYZ Helps Horton Fulfill Lean Manufacturing Goals
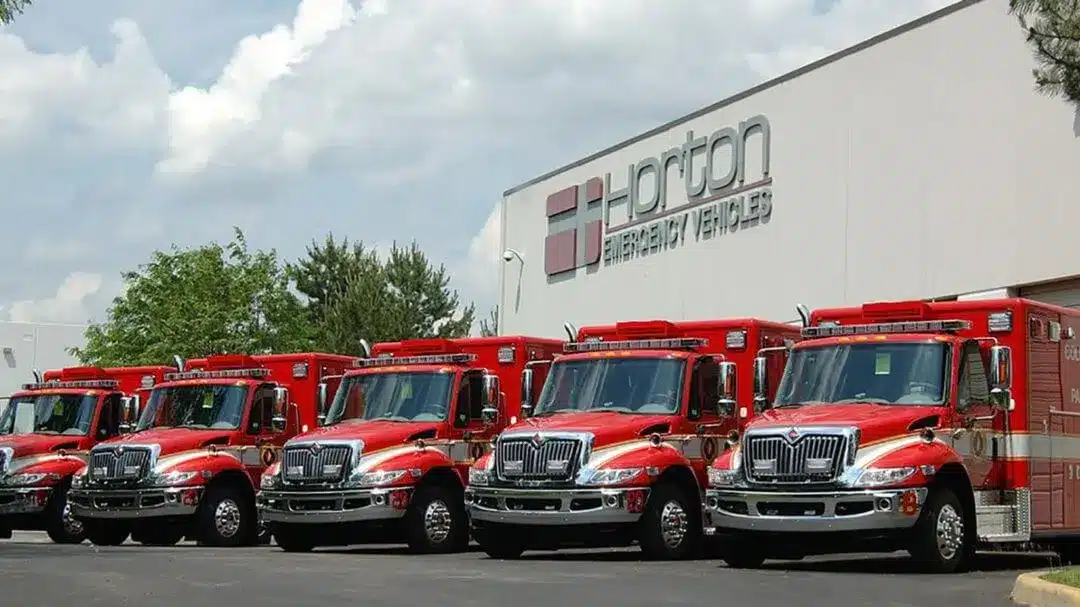
How does an established and successful company change their entire manufacturing process? By adopting lean manufacturing principles, and with the help of a state-of-the art router from AXYZ.
Driving Innovation
Horton Emergency Vehicles has a history of innovation. In fact, the concept of the modern ambulance, outfitted with state-of-the-art life-saving equipment, was the brainchild of Carl Horton, who founded the company in 1968. Now part of Allied Specialty Vehicles, Grove City, Ohio-based Horton is in the business of building emergency vehicles, including ambulances, critical care transport and rescue vehicles. Completing, on average, two vehicles each working day, they recently sold their 16,000th vehicle. Their products help save lives all over the United States, and in the United Arab Emirates and Switzerland.
A Process Change
Even though Horton was a successful company, they saw a need to streamline manufacturing processes, changing from a bay-build facility to a lean manufacturing system. Pioneered by car company Toyota in the 1980s, lean manufacturing focuses on minimizing waste while improving value. “In our old process an ambulance would pull in to a designated bay where it would sit stationary from 3 days to 45 days while being worked on,” explains Ricky Loar, Horton’s senior operations and plant manager. “Time was not a critical factor due to build length times. If an item took 12 hours, then it took 12 hours.”
But with the switch to lean manufacturing, time spent constructing components became vital. Horton performed time studies to analyze the optimal time to complete each step in an ambulance build, and then created a standard workbook with best-case times. “We asked: ‘How could we do things better based on the operational excellence in lean manufacturing?’ We were definitely looking for more efficiency, taking labor out of the product,” says Loar.
A New AXYZ Router Helps Streamline Processes
But they discovered that their existing machinery wasn’t up to the task of adapting to the needs of their new manufacturing paradigm. “We were having difficulty with process lead time and trying to fit into a particular takt time,” says Loar. “Our plant cycles every 277 minutes, which means no job can take longer than 277 minutes to complete. We had 10 jobs with long lead times that we could just not figure out how to fit into that base takt. So we started looking at alternatives.”
horton2One of the main problems was that some elements were still being done manually, and in individual components. “Some things like our ambulance walls, roof panels, carbon fiber material, and Plexiglas cabinets, for example, had engineering drawings, but the finish work with a routed edge was still done by hand,” says Loar. For example, the Avonite Countertops required several, labor-intensive steps, averaging 12 hours of production to complete a single tray.
They realized they could increase their efficiency if all those elements could be done in large lot sizes. After researching the available routers, they chose the AXYZ 6012 CNC Router from Burlington, Ontario-based AXYZ, the leading supplier of high-performance routing, cutting and engraving solutions to the Plastics, Signmaking, Woodworking and Metal Fabrication industries.
AXYZ’s range of CNC Routers come in 4000, 5000, 6000, 8000, and 10000 Series machines in a wide range of configurations. The AXYZ 6000 Series CNC Router delivers the largest processing area for this style of machine on the market. The 6012 in particular offers an 85” (2159mm) by 144” (3658mm) processing area to ensure materials will fit without the need to cut them down. They’re also often built with automatic vacuum zone switching to enable continuous operation on multiple sheets of material. AXYZ 6000 Series machines are popular choices for industries like signmaking, solid surface fabrication, aluminium fabrication, and woodworking.
Production Times Cut, Money Saved
Once the AXYZ CNC 6012 was up and running, Horton was able to drastically cut down production times. Now, an Avonite Countertop takes a mere 4 hours,” saysLoar, and all the work is done at a single station. Special cuts and angles are incorporated into renderings that are sent directly to the CNC Router 6012, with little to no material waste. Loar estimates that the company saved 60 to 73 hours with each vehicle, depending on the truck model, which paid for the router in less than a year. “We actually saved even more than we thought we could,” he says.
Horton purchased the training package for the router, a 2-day program, which, for Horton, focused on ArtCAM, the design, modeling, and machining software. “One of the things we really like is the computer-driven accuracy,” says Loar. “The fact that I can call something up, send it directly to the machine, hit go on my computer and have the part waiting for me when I get out there is great.”
While Horton had some computer issues with their existing program, AXYZ has worked with Horton to troubleshoot and correct the problem. “I called in and explained the problem to AXYZ. They actually worked with our IT department to correct the issue on our end to make sure it never happens again,” says Loar.
Leaning Into the Future
Horton Emergency Vehicles continues on its journey of implementing more lean manufacturing processes into its workflow, and possibly adding yet another AXYZ Router to their lineup to create even more efficiencies. So far, the company’s progress has been testament to their commitment to change. The average company takes about 7 years to fully execute a lean system, says Loar, and Horton has managed to do it 3 years. “We’ve been extremely successful over the last couple of years and this third year we can really see a tremendous difference here at Horton,” says Loar. “The real cornerstone of lean manufacturing is operational excellence and this router has helped Horton live up to that process.”
Get in touch
Product Brochures
Get a copy of AXYZ’s latest product brochure. Learn all about our extensive range of AXYZ CNC Routers. Choose between our six major brands – INFINITE, INNOVATOR, METALWORKER, TRIDENT, WOODWORKER and PANELBUILDER.